Introduction to MVR Technology
Mechanical Vapor Recompression (MVR) has revolutionized industrial evaporation processes by slashing energy consumption and operational costs. Unlike traditional methods that rely on steam, MVR systems reuse vapor, making them ideal for sectors like chlor-alkali, lithium extraction, and wastewater treatment. At the heart of these systems lies a critical component: the evaporation axial flow pump. This article explores the MVR evaporator working principle and how high-performance circulation pumps drive efficiency and reliability.
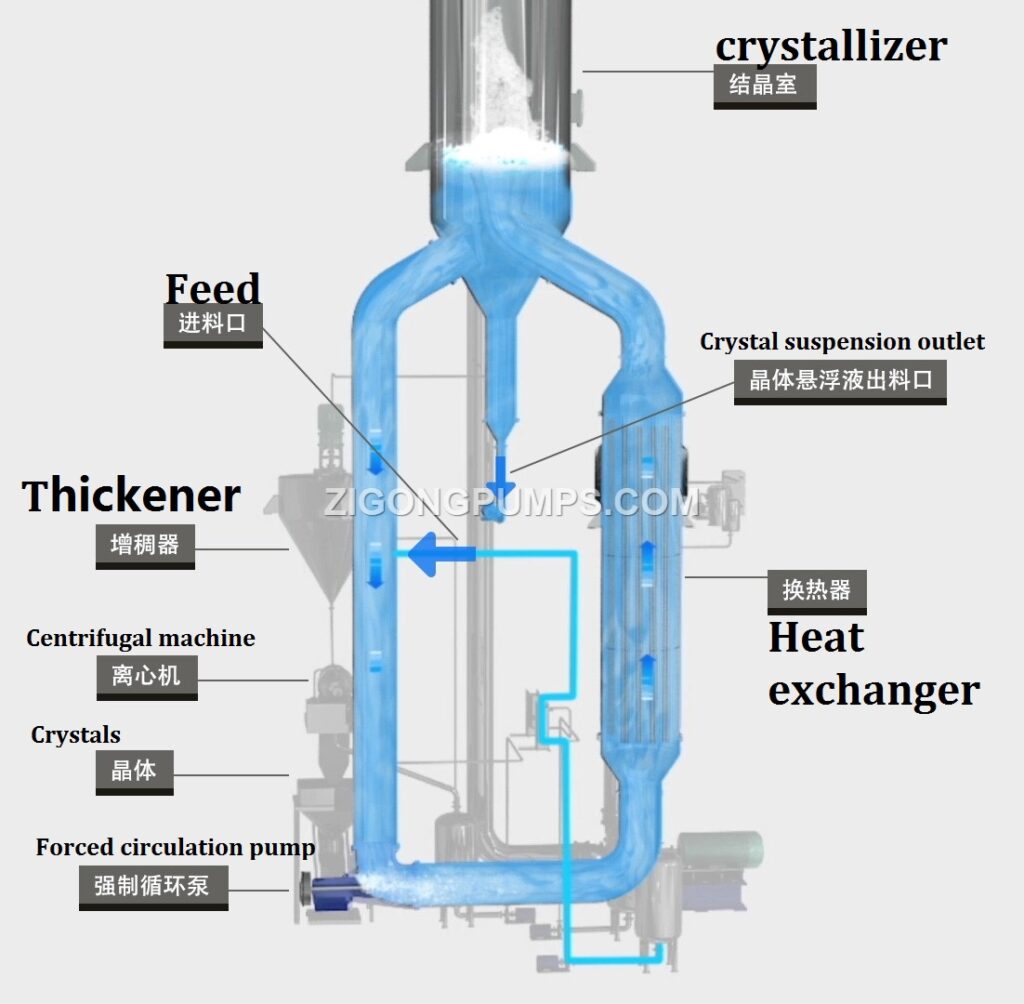
Understanding the MVR Evaporator Working Principle
MVR technology recovers and recompresses vapor to elevate its temperature and pressure, transforming it into reusable thermal energy. Here’s a step-by-step breakdown:
- Evaporation: Liquid feedstock is heated, generating vapor.
- Vapor Compression: A mechanical compressor recompresses the vapor, boosting its energy.
- Heat Reuse: High-energy vapor condenses in a heat exchanger, transferring latent heat to the feedstock.
- Continuous Cycle: The process repeats, minimizing external energy input.
This closed-loop system thrives on components like compressors, heat exchangers, and forced circulation pumps, which ensure seamless operation.

Key Components of an MVR System
- Compressor: The core of vapor recompression.
- Heat Exchanger: Facilitates energy transfer between vapor and liquid.
- Evaporation Axial Flow Pump: Drives high-volume fluid circulation, maintaining optimal heat exchange and preventing scaling.
Why MVR Outperforms Traditional Evaporation
- Energy Efficiency: Up to 90% reduction in energy use by recycling vapor.
- Cost Savings: Lower operational expenses and smaller carbon footprint.
- Scalability: Adaptable to industries from pulp/paper to lithium extraction.
The Critical Role of Evaporation Axial Flow Pumps
In MVR systems, circulation pumps (or forced circulation pumps) are indispensable. Here’s why:
- High Flow Rates: Ensure rapid fluid movement through heat exchangers, maximizing thermal transfer.
- Corrosion Resistance: Built to handle aggressive fluids in wastewater or chlor-alkali applications.
- Thermal Stability: Operates efficiently under extreme temperatures common in lithium extraction.
- Durability: Reduced maintenance needs and extended lifespan, even in abrasive environments.
Applications Across Industries
- Chlor-Alkali: Manages corrosive brine solutions with precision.
- Lithium Extraction: Withstands high temperatures during mineral processing.
- Wastewater Treatment: Handles viscous, particle-laden fluids without clogging.
- Pulp & Paper: Maintains consistent flow in high-demand evaporation stages.
Why Choose Our Evaporation Axial Flow Pumps?
Our pumps are engineered to excel in MVR environments:
- Custom Design: Tailored to meet specific flow and pressure requirements.
- Energy Optimization: Reduces power consumption while boosting output.
- Robust Construction: Materials like duplex stainless steel combat corrosion and wear.
- Expert Support: Decades of expertise in serving MVR and heat exchanger industries.
Conclusion: Power Your MVR System with Precision
Understanding the MVR evaporator working principle underscores the importance of reliable components. As industries prioritize sustainability and cost-efficiency, integrating high-quality axial flow pumps becomes paramount. Whether you’re upgrading an existing system or designing a new one, our evaporation crystallization pumps deliver unmatched performance.